When business owners want to install a refrigerator line, they must look for a reputable supplier with the best equipment in the industry. This includes conveyor belts, thermoforming and PLC controls, as well as ensuring all components are tested for electrical continuity and safety.
Transmission lines
The invention relates to a refrigerator production conveying line. It aims to provide an easy and efficient way to deal with various types of devices. In addition to the conventional delivery system, the present invention also includes a scanning device, a local server and a power supply device.
Scanner devices can be wired or wirelessly connected to a local server. The device scans the product identification code obtained from the local server. The control module analyzes the code and sends a request to the local server to update the assembler firmware.
The control module uses an appropriate program to calculate the most efficient way to obtain the identification code. When the assembled refrigerator enters the product control area, the product control device is activated.
The local server obtains the address code of the assembled appliance and sends the firmware update package to the correct location in the refrigerator. Firmware update packages include software and hardware upgrades that enhance device performance.
The local server also obtains a more accurate identification code from the second scanner device. Equipped with a microcontroller, the device can transmit data to a local server either wired or wirelessly.
Finally, the power supply unit is designed to provide continuous power to the assembled refrigerator. Depending on the size of the utensil, different types of chains are used. Among them, the light plate chain conveyor is typically used in the home appliance manufacturing industry. Their station load capacities vary from 100kg to 2 tonnes.
One of the coolest features of the line is its flexibility. When the model of refrigerator changes, the wiring can be adjusted to accommodate the change.
Thermoforming
There are many common thermoforming methods. These include mechanical forming, pressure forming and vacuum forming. Thermoforming is used for plastic materials which are then molded into various appliances. It is also used in the manufacture of disposable products for the food industry.
Thermoforming is typically applied to thin gauges such as blisters and lids, as well as trays and swizzle sticks. However, thick-gauge thermoforming is also used to manufacture a wide range of parts, from refrigerator liners to tractor interiors. This method uses a sheet of heated plastic material, which is then pressed against a mold.
One type of thermoforming process involves the use of twin sheets. In this process, the upper and lower plates are integrally formed to define a support surface. Additionally, the clamping frame and upper ring frame member are also attached to the upper platen.
Another process involves using a single sheet of paper, which is heated in an oven to high temperatures. The plastic is then stretched over a mold into the desired shape. After the part cools, it is trimmed to its final shape.
Thin gauge thermoforming requires specialized equipment. Thermoforming machines are available for desktop and industrial applications. Many of these machines are equipped with heating and cooling systems, forming areas and electrical control systems.
Heavy gauge thermoforming is ideal for large, heavy panels such as refrigerator liners, trailers and truck cabs. It is also used in bathtubs, car door panels and cargo box liners. While high quality is required for this process, it is a cost-effective option, especially for larger items.
Large thermoforming is typically used in production quantities of 250 to 3000 pieces per year. This is a faster and cheaper process than other plastic technologies. Typically, thermoformed parts are hand-machined after forming and may require additional finishing.
PLC control
A study was conducted to determine the availability of a refrigerator production line using PLC. The study found that 84% of production lines are running at all times. This compares to a 24 percent failure rate when using a control system that does not include a PLC.
Developed a control system including touch screen, communication board and Siemens series PLC. These components are connected to the IoT module, PID controller and operator panel.
The touch screen allows users to view and manipulate experimental data. The operator panel displays real-time data, and a PLC connected to the building's Ethernet system allows users to remotely monitor and troubleshoot the production line.
The TIA Portal V16 software application was used to configure the PID controller to handle the compressor speed control program. The software tool provides the user with a number of predefined standard function blocks.
Tested for electrical continuity and safety
When your refrigerator production line is ready to ship, it needs to be tested for electrical continuity and safety. This is important because if the equipment fails, it could be a hazard to your health and could lead to a major failure.
To be safe, you should thoroughly test all electrical components, including wires, cables, and connectors. If defects are found, it's time to replace them.
Additionally, a high voltage test may be required to ensure that the insulation is intact. Testing can reveal gaps in insulation, humidity and manufacturing failures.
Typically, this type of test is performed at twice the normal operating voltage. This helps avoid tripping the circuit breaker and ensures that all voltages in the enclosure are safe.
Another test is the insulation resistance test. These tests measure the insulation resistance of a 230-volt power supply. An open circuit can cause high readings, which is a sign of insulation failure.
If you're testing insulation, be sure to choose a dedicated tester. These devices have a light bulb that indicates the current.
If you don't use a dedicated test, you can use a multimeter for continuity testing. However, this is not recommended.
For enhanced continuity testing, use a PC-based cable tester. PC-based testers are designed to accommodate long test interfaces and are ideal for design verification and prototyping.
It can be integrated into an environmental chamber test system using a PC-based tester. Environmental chambers simulate the lifetime of a product, making it easier to detect design flaws.
Continuity testing can also be performed with a digital multimeter. The multimeter has a continuity test mode that can be used to check electrical connections and fuses.
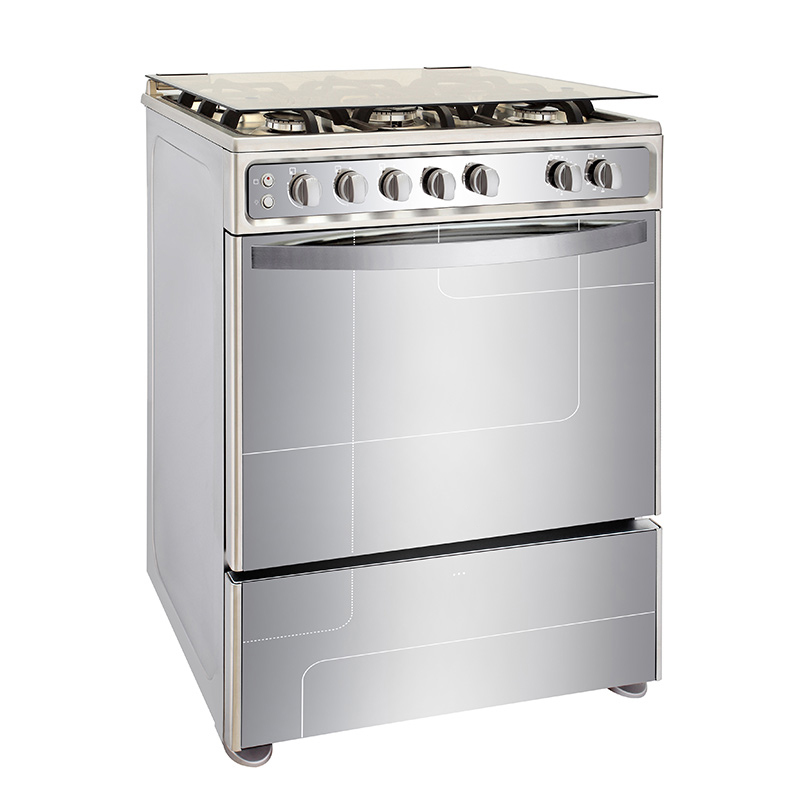
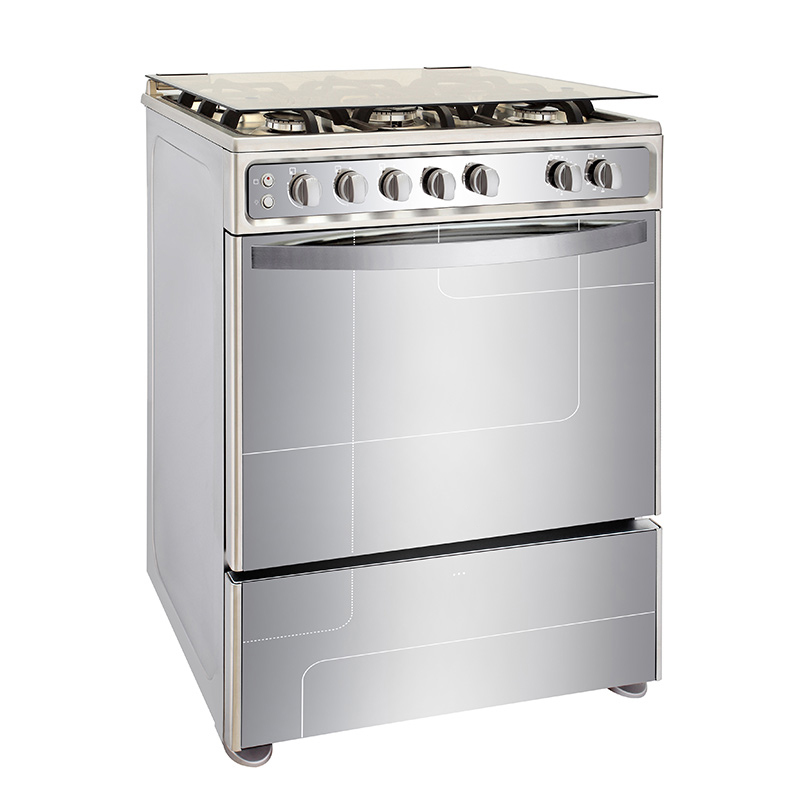
Usage:
Plastic pallets are commonly used for the commercialization of high rotation and/or bulky products. These pallets reduce the risk of damaging a product by moving it from one point to another. This is because you will only lift the platform without touching the product.
Advantage of plastic pallet:
easier to transport.safer for everyone.take up less space.more flexible and versatile.have a longer lifespan than wood pallets.