The Art of Precision: Optimizing Efficiency in Refrigerator Manufacturing
Manufacturing refrigerators requires a meticulous and well-orchestrated production line that ensures efficiency and consistency throughout the manufacturing process. The first step in optimizing efficiency is the careful design and layout of the production line. Every aspect, from raw material handling to assembly and packaging, must be strategically organized to minimize downtime, reduce waste, and maximize productivity.
To achieve this, manufacturers implement lean manufacturing principles, which involve eliminating unnecessary steps, optimizing workflow, and implementing automation where appropriate. By leveraging advanced technologies and automated equipment, manufacturers can streamline processes, improve production speed, and reduce the likelihood of human errors. Additionally, thorough training programs and quality control measures are implemented to maintain high standards at each stage of the production line.
Ensuring Quality from Start to Finish: Stringent Standards in Refrigerator Production
Refrigerators are complex appliances that require precision engineering and rigorous quality control measures to meet industry standards and customer expectations. From the selection of raw materials to the final inspection of the finished product, every step of the refrigerator production lineis closely monitored to ensure the highest level of quality.
Quality control begins with stringent material testing and inspection procedures. Components such as compressors, condensers, and insulation materials undergo rigorous evaluation to verify their performance, durability, and safety. Throughout the assembly process, quality checkpoints are established to detect any potential defects or malfunctions. These checkpoints often include performance tests, temperature measurements, and functional assessments to ensure that each refrigerator leaving the production line meets or exceeds the specified requirements.
Continuous Improvement: Embracing Innovation in Refrigerator Manufacturing
Refrigerator manufacturers understand the importance of staying ahead of the curve and embracing innovation to remain competitive in the market. Continuous improvement is a key focus in the production line, with manufacturers actively seeking ways to enhance their processes and incorporate the latest technological advancements.
By leveraging data analytics and real-time monitoring systems, manufacturers can gather insights into the production line's performance and identify areas for improvement. This data-driven approach enables them to optimize production schedules, identify bottlenecks, and implement corrective measures promptly. Furthermore, manufacturers collaborate with suppliers and research institutions to explore new materials, energy-efficient technologies, and smart features that enhance the functionality and sustainability of their refrigerators.
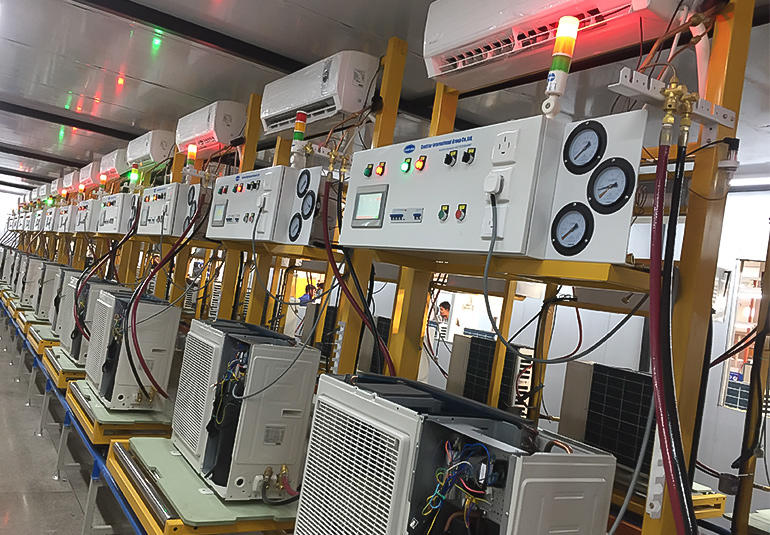
Main Target Markets
Mainland China, Africa, Middle East, Southeast Asia, South Asia, Latin America, Russia, European countries, Australia and other regions
Refrigerator solution description:
According to household electrical appliance products’ assembly process flow and plant features, plan the production line layout, offer appropriate type of conveyance line and realize the streamlined production of the whole production process, such as pre-assembly, vacuum-pumping, refrigerant charging, safety check, leakage check, performance inspection, packaging and packing. The line can be used for two production modes (SKD and CKD) according to customer budget and part type. The conveyor line can be controlled automatically with PLC with variable speed and stable conveyance.
Based on refrigerator assembly process flow and plant details, plan the production line layout in