Freezer CKD supply refers to the supply of Completely Knock Down (CKD) units for freezers. CKD units are partially assembled products that are shipped in parts and assembled at the final destination. Freezer CKD supply typically includes all the necessary components and instructions for assembly, but not the final packaging or branding. This is a common practice in the manufacturing industry, as it allows for greater flexibility in terms of customization and localization.
The use of freezer CKD supply can be beneficial for a number of reasons. One of the main benefits is cost-effectiveness. Shipping partially assembled products reduces the cost of transportation, as more units can be packed in a container, and it also reduces the import duties. Additionally, assembling the units at the destination can also save on labor costs.
Another benefit of freezer CKD supply is localization. Assembling the units at the destination allows manufacturers to customize the product to suit the local market. This can include adapting the product to local electrical standards, adding local language instructions and labeling, and making any other necessary modifications.
Furthermore, using CKD supply allows manufacturers to respond more quickly to changes in demand. Assembling units at the destination allows for a shorter lead time and more flexibility in terms of production. This can be particularly important for companies that operate in fast-moving consumer goods markets.
Overall, the use of freezer CKD supply allows manufacturers to reduce costs, customize the products to the local market, and respond more quickly to changes in demand.
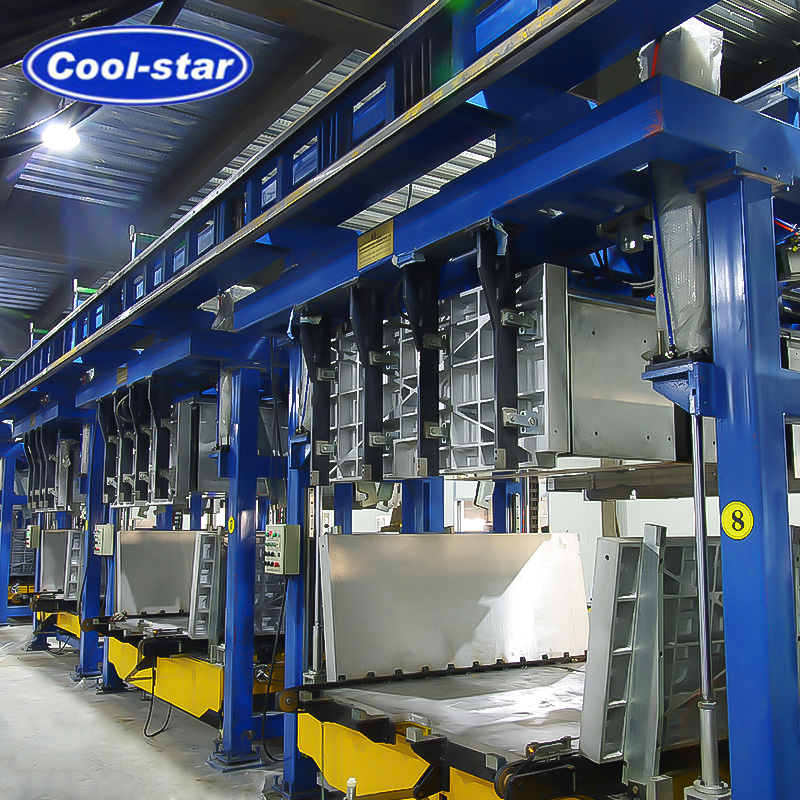
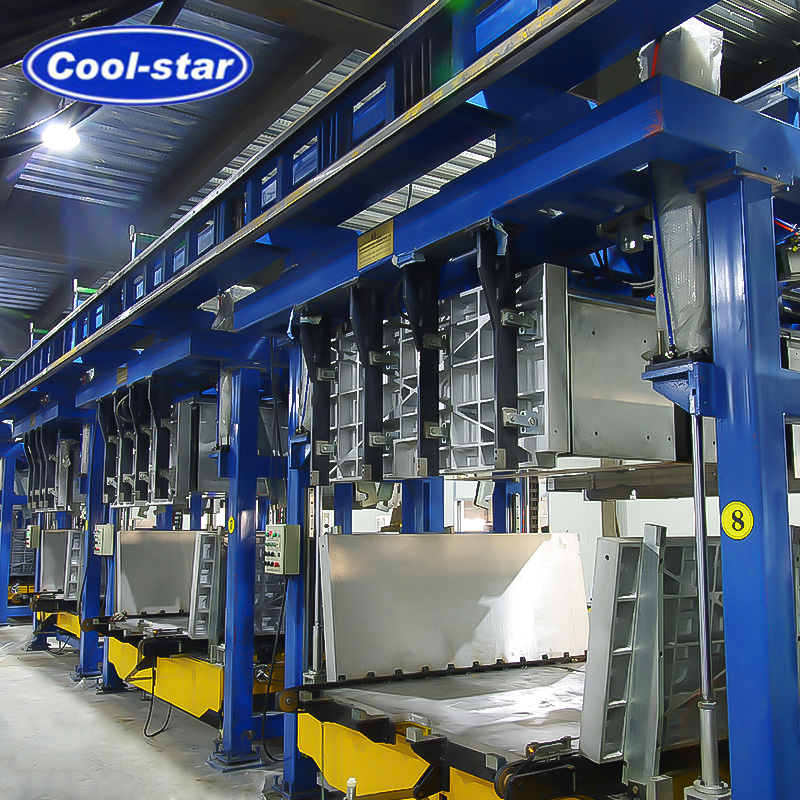
Foaming Line Equipment (Dry Part):
As dedicated equipment of refrigerator foaming, the equipment is mainly used in the foaming process of refrigerator to complete cabinet or door’s automatic positioning, automatic clamping, automatic mould locking and automatic charging to ensure that cabinet or door will not deform in the overall foaming process. Dry part of refrigerator foaming mainly comprises mould frame, automatic injection system, water circulation temperature control system, mould change trolley, hydraulic system, safety exhaust system, electric control system, and bidirectional carrying trolley or lifting translation conveyor line (either), which are generally arranged linearly and combined with assembly line to realize the streamlined production. Dry part of door foaming, adopting rotary type generally, is mainly consisted of main frame, rotary disk, foaming mould frame, drive device, indexing positioning device, open/close device, mould supporting device, automatic charging system, water heating system, safety exhaust system, hydraulic system and electrical control system. Depending on budget and cycle time, either linear type or ground rail type can be adopted.